How Did They Build That? John Hancock Center, Chicago
It is an innovation in skyscraper engineering, the first building to combine residential and commercial space together, the thirteenth largest building in the United States…Chicago’s skyline wouldn’t be the same without this architectural and structural icon.
The John Hancock Center “…will always be something for people to reach for. It’s a clarity and simplicity and expressiveness and the story it tells is just timeless.” -SOM structural engineer and Burj Khalifa engineer, William F. Baker

The John Hancock Center—now named 875 North Michigan Avenue—in downtown Chicago, Illinois, is the highly successful collaborative effort of architect Bruce Graham from Skidmore, Owings & Merrill, structural engineer Fazlur Rahman Kahn, (original) owner Jerry Wolman, the John Hancock Mutual Life Insurance Company, and the Tishman Construction Company. The vision, revolutionary ideas, and expertise between these different companies and people paved the way for the modern construction of the world’s tallest buildings.
How can collaboration in construction lead to growth? Click here to find out.
The Vision
The original project owner of the John Hancock Center was Jerry Wolman (1927-2013), a builder and real estate developer who became known as the youngest owner in the NFL when he purchased the Philadelphia Eagles in 1963. In 1964, Jerry set out to build the world’s tallest building, investing $22 million of his own money.
Originally meant to be two buildings—one residential and one commercial, after surveying the area, one building that stood in the development’s plan refused to sell. This turned out to be a blessing in disguise, however, as the architects said the two-building plan would block natural light and views for both buildings. Also, the vision to combine the two spaces into one building led to innovation in high-rise building construction.
Influential architectural firm Skidmore, Owings & Merrill (now SOM) took on the project with their architect Bruce Graham and structural engineer and partner, Fazlur Rahman Khan.
Construction of the John Hancock Center began in 1965; however, was stopped in 1967 because the building kept sinking. Because of the John Hancock Center's lakeside location, 57 concrete caissons had to be sunk into 10 ft wide holes drilled 197-feet below grade into bedrock, resulting in the John Hancock Center having the deepest foundation of any building at the time.
Because of this, Wolman could no longer afford the construction. Wolman walked away from the project and investors John Hancock Mutual Life Insurance Company took over.
Never done before, combining the two buildings would be challenging, as residential buildings are traditionally designed for smaller floorplans and to maximize the natural light and optimize views, while commercial buildings are generally designed for larger floor plans.
The Expertise
Skidmore, Owings & Merrill (SOM)
Founded by architects Louis Skidmore and Nathaniel Owings in Chicago in 1936, engineer John O. Merrill joined the company in 1939. With offices now all over the world, SOM is noted as one of the first American architectural firms to introduce art in their design with the 1952 completion of Lever House in New York City. Made of steel and glass in a sea of brick, Lever House was the first international-style tall building in New York City.

Another notable first was the company’s early sustainable building designs. What is possibly the first green building, SOM integrated the 1971 Weyerhaeuser Company headquarters into the natural landscape reducing environmental impact and incorporated efficient building practices. They also designed the first building to receive LEED certification—the U.S. Census Bureau headquarters. The company also designed one of the world’s first zero-energy buildings, The Kathleen Grimm School for Leadership in Sustainability in New York City.
Further evidence of the innovative spirit from SOM was their eagerness to embrace new technologies. They developed their own computer-aided design systems before CAD. A department at SOM called the Computer Group utilized computer systems to store and recall accurate data throughout their process. Similar to the construction software we have today—like Beck Technology’s DESTINI Estimator—the SOM Computer Group was able to produce calculations quicker, as well as share information in ways not done before. In fact, the Computer Group team developed a program called Architecture Engineering Systems, the forerunner of current BIM tools.
Bragging? Don't mind if we do! Click here to read about one of our client's most innovative projects, Reunion Tower in Dallas, Texas.
Other significant buildings designed by SOM are The Walt Disney Company headquarters, PepsiCo corporate headquarters, Moon Village—the first concept in lunar living, Willis Tower, One World Trade Center, and the world’s tallest building, Burj Khalifa.
Fazlur Rahman Khan
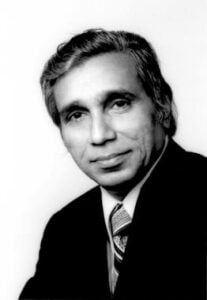
Structural engineer and architect pioneer, Fazlur Rahman Khan, worked alongside architect Bruce Graham to develop a revolutionary idea on how to build this high-rise building.
Born in what is now Bangladesh, Fazlur got his bachelor's degree of civil engineering from Ahsanullah Engineering College and after becoming a Fulbright Scholar, received two master’s degrees—structural engineering and theoretical and applied mechanics, and a Ph.D. in engineering from the University of Illinois at Urbana-Champaign.
He began working at Skidmore, Owings & Merrill in 1955 where he developed the tubular construction method for tall buildings. The first building to incorporate this revolutionary design was the travertine marble-covered DeWitt-Chestnut Apartment Building in Chicago completed in 1966.
The Revolutionary Ideas
Tube Structural Systems
Inspired by the hollow tube of the bamboo that grew in his hometown of Dhaka, Fazlur introduced his innovative trussed tube structural system in the design of the John Hancock Center. Fazlur defined his tube method of building high rises as “a three-dimensional space structure composed of three, four, or possibly more frames, braced frames, or shear walls, joined at or near their edges to form a vertical tube-like structural system capable of resisting lateral forces in any direction by cantilevering from the foundation." ("Structural Systems," Tall Building Systems and Concepts, Council on Tall Buildings and Urban Habitat/American Society of Civil Engineers, Vol. SC, p. 42, 1980.)
The tube structural system developed by Fazlur is what allows super tall buildings to remain structurally sound, while reducing the amount of steel used. The X-bracing truss system eliminates the need for inner support columns and directs lateral loads to the exterior columns. Though the trusses interrupt views and block windows, it does open the interior to best maximize floor space.
One of John Hancock Center’s greatest distinctions are the large diagonal bracing trusses on the outside of the building. Based on the trusses used in bridge construction, Fazlur used them to reinforce the tube structure, making it more structurally sound. Omrania writes, “Instead of relying upon a conventional steel frame system, he pushed most of the structural elements to the perimeter, so that the entire building would behave structurally as a hollow tube—reducing the amount of steel by nearly 50%, lowering building costs, and creating more open interiors.” (How the Hancock Center and Tube Structures Changed Skyscraper History - Omrania)
SOM writes, “Structurally, the steel frame’s exterior members represent a tube where the necessary stiffness is provided by diagonal members and those structural floors that coincide with the diagonals’ intersections and the corner columns. In keeping with the functional organization, this tubular body has its largest cross-section where the stresses caused by wind forces are greatest. Steel consumption, amounting to about 30-pounds-per-square-foot of floor space, was no greater than for a 50-story conventional tower.”
The unique taper of the building further allows for better use of the floor space for the office spaces on the lower stories and residents on the upper, presents an illusion of even greater height (like it needed it!), was an efficient use of steel (making the project cheaper), and further reduced surface and wind loads—a crucial element for skyscrapers in the Windy Cindy.
Most skyscrapers and supertall buildings are still built using Fazlur’s tube system.
17 Interesting Facts About the John Hancock Center
- On a clear day, you can see up to 80 miles and 4 different states from the top.
- At the time, it was the second building ever to reach 100 stories.
- If measured to the top of the antennas, it stands 1,500-feet tall.
- It is the 33rd tallest building in the world.
- With 700 apartment spaces, it is the third highest residence in the world.
- The elevator is said to be the fastest in the United States at 20 miles per hour.
- In 1999, the building received the Distinguished Architects Twenty-five Year Award from the American Institute of Architects award.
- It took over 2,000 construction workers and five million hours to complete the building.
- The steel in the building’s frame, which weighs 46,000 tons is enough to make 33,000 cars.
- Used only in the construction of bridges previously, creeper cranes were used to hoist the steel beams in place.
- Each of the building's X-shaped trusses are 18 stories high.
- Way before its popularity, Fazlur was a fan of prefabrication and all the joint assemblies were prefabricated, eliminating the need for field welding.
- The apartments have radiant heat in the ceilings.
- When completed in 1969, it was the world’s second-largest building.
- The 44th floor holds the country’s highest indoor swimming pool.
- Fazlur was concerned about residents feeling the movement of the building, so after visiting the Museum of Science and Industry in Chicago, he developed a test to make sure those living in the John Hancock Center would feel no discomfort during strong winds.
- Fazlur and Bruce worked closely together for the rest of their careers and are buried next to each other in Chicago’s Graceland Cemetery.
Finally completed in 1969 and affectionally nicknamed “Big John” to locals, the iconic John Hancock Center—or 875 North Michigan Avenue—is proof that collaboration and a passion for innovation between owners, architects, engineers, contractors, and subcontractors are what pushes the industry into new heights.
For more How Did They Build That series, click the picture below: