Exciting Construction Trends: Prefabrication
In recent years, the construction industry has been overflowing with incredible innovations, new technology, and exciting trends. From the rise of BIM estimating to mapping out construction sites with drones, no aspect of the industry has gone untouched by the creative solutions and pioneering spirits of the people within it.
One of the most interesting trends that is becoming increasingly common is prefabrication work. Prefabricated construction, also known simply as “prefab,” is a method of construction in which a building’s components are created offsite—typically in a factory—and then assembled at the project site. Although prefabrication has existed for centuries, it has only become more common recently due to technological advancements that now enable much faster component creation, to the point that even buildings with multiple stories can be prefabricated.
Prefabrication brings many benefits as opposed to more traditional methods of construction. But before examining why it’s often a better choice for both contractors and project owners alike, it’s important to understand how prefabrication emerged into the industry and why it’s being adopted so frequently now.
The History of Prefabrication
Prefabrication would seem to be a modern concept at first glance, but the techniques that inspired prefabricated construction date as far back as Mesopotamian civilization. The first “true” prefab was a house created for a fishing fleet in Massachusetts; the house was built in and then shipped from England. From the start, prefabrication was primarily used for residential developments.
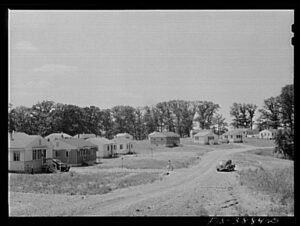
In 1830, a carpenter from London, Henry Manning, developed a wooden cottage that he specifically advertised as prefabricated and shipped it to Australia. Meanwhile, the California Gold Rush spurred on prefabricated work in America, with railroads serving as an accessible way to ship kit houses to settlers laying down roots in the West. Just a few decades later, prefabrication helped tackle the massive problem of housing shortages in Europe that arose from the destruction of World War I.
Prefab homes were also becoming very popular in America. Buckminster Fuller was one of the first to come up with the idea of a metal-dome residence that could be quickly disassembled and then transported. Other developers took their own spin on this idea, and one of them, William Levitt, actually created homes that could be built in just sixteen minutes. By the time the 1960s rolled around, mobile homes made up fifteen perfect of the housing in the United States.
Unfortunately, although prefab work saved money and time, the designs were not particularly attractive to the average consumer. As a result, prefabrication experienced a fall in interest as people turned to favoring more unique and aesthetically appealing residences.
But in the early 2000s, new developments brought a resurgence of prefabrication work. Technologies like 3D printing and building information modeling (BIM) made it possible to scale prefabricated work to projects beyond homes; now, constructions like bridges and office buildings could be created with the prefabrication method.
Benefits of Prefabricated Construction
It’s clear that prefabricated work has been extremely popular for a while, and that trend is only continuing to move upwards. In fact, according to the UA Builders Group, prefabricated construction is expected to increase six percent globally by 2022.
While there are still many situations in which traditional construction methods are still very necessary, there are two huge reasons why a general contractor might want to consider prefabricated work first:
- To save on costs, both material and labor
- To become more competitive and grow faster
To save on costs, both material, time, and labor
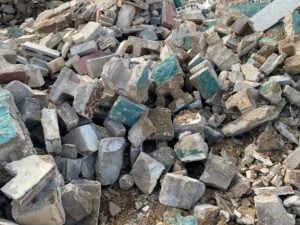
Prefabricated construction saves a lot on costs to a contractor due to the simple fact that because it relies on repeatable materials created offsite, it makes it much harder to misplace or lose materials in the field, thereby significantly reducing waste. This is huge for contractors: several studies have found that on average, most construction projects in the U.S. go over budget by at least sixteen percent.
In addition to helping contractors stay within budget, prefabrication also minimizes the blow from labor shortages since it doesn’t require as many hands on deck. It also gives contractors much more control over both quality and consistency, significantly cutting back time that might have otherwise been wasted on trying to correct mistakes.
To become more competitive and grow faster
As mentioned above, since the early 2000s prefabrication was largely the realm of residential development and civil engineering. However, prefabrication holds a lot of possibilities for commercial construction as well. Many commercial projects rely on repeating steel elements as well as glass panels, both of which are much easier to mass-produce via prefabrication.
Prefabricated work also goes up far more quickly than most traditionally built projects: Autodesk estimates that prefab buildings can go up as much as fifty percent faster than traditional buildings. All that time gives contractors the ability to turn around and complete more projects, enabling more return on investment and faster growth for the company.
Technology Enables Success
Technological advancements have put prefabrication in the spotlight, in much the same way they have for preconstruction, too. Developments like all-in-one estimating software, data visualization models, and historical cost analysis have all helped completely transform preconstruction initiatives.