How Major Events Shape Construction
We’ve talked a lot about how construction shapes the world around us. But the reverse is also true: what happens outside of construction can also impact its trends and evolution. You probably remember learning in history class about how technological advancements during the Industrial Revolution led to huge factories and crowded living spaces, and how the subsequent negative effects such as increased illness, environmental pollution, and greater automation then led to the collapse of most factories and a move toward more sustainable housing and planned communities. Even today, recent events are a huge testament to the way the outside world can transform the construction industry.
The problem with trying to analyze the impact of current world phenomenons is just that: they’re current. It’s difficult to fully realize the ripple effect they will bring when you are literally living through them. On the other hand, looking at the past too broadly makes it hard to gain truly fulfilling and useful insights. Focusing on specific, major events that happened about 10-50 years ago is a much better way to grasp the surprisingly long-lasting trends they set upon the industry.
There are three milestone events that have shaped the construction world we move through today:
- World War II and modular construction
- Federal Highway Act of 1956 and interstate construction
- 9/11 and building codes
World War II and Modular Construction
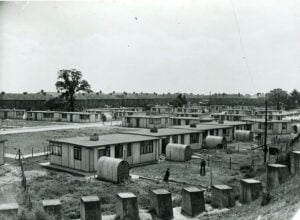
Modular construction, also known as prefabricated construction, is the process in which repetitive sections known as “modules” are constructed away from the building site under controlled conditions before being delivered to the building site for installation. Although modular construction certainly existed in the United States prior to World War II, it did not become popular until the war’s conclusion.
Prior to the war breaking out in 1939, U.S. homeownership was at an extreme low of 43.6% due to the aftereffects of the Great Depression. As the war gained steam, the U.S. War Production Board placed construction under tight regulations via Conservation Order L-41. This order was intended to refocus efforts toward developing armament factories and military bases and wasn’t revoked until October 1945, about five months after the war had ended.
In those five months, the U.S. was faced with two major problems. First, there were millions of soldiers returning home, many of them married and ready to start their families. However, the U.S. was wildly unprepared for their return: there were simply not enough homes ready for them. There was also absolutely no way that the necessary amount of homes could be built in a short timeframe using current methods; one article predicted, “It will be ten years before the whole nation is properly housed.”
The second issue was that dozens of wartime companies were beginning to struggle now that their contracts had been canceled. These companies had gained an incredible amount of fabrication experience involving materials like aluminum and steel, but since military production had drastically scaled back, they were left with nowhere to use these skills.
As a direct response to World War II and the need that its completion created, prefabricated housing erupted as the solution to both of these problems. Former war companies utilized their prior experience to mass-produce houses—many of them primarily or even wholly composed of aluminum—for veterans looking to lay down roots. The boom in prefabricated housing quickly led to the emergence of what we know as “suburbia”, or planned communities. As a result, prefabrication started to become more and more commonplace not just in residential construction, but also in traditional vertical and commercial construction as a way to save more time and more money.
Federal Highway Act of 1956 and Interstate Construction
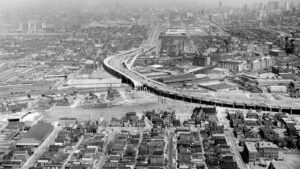
As the dust from World War II began to settle and the U.S. began to return to peacetime, its leadership looked for ways it could continue to shore up its defenses in the meantime. One of the steps they took toward this goal was the introduction of the Federal Highway Act of 1956. This act—also frequently referred to as the National Interstate and Defense Highways Act—authorized $25 billion for 41,000 miles of the new Interstate Highway System.
Thanks to this commission, heavy construction began booming in the 1960s and quickly impacted the types of equipment that were usually employed for these kinds of projects. Machines like shovels and haul trucks got bigger and more powerful in order to handle the incredible amounts of materials that construction crews were faced with. This would be the largest that the industry would ever see them—machines have no longer become bigger, but instead more efficient.
The other change that the Federal Highway Act brought to construction was a major improvement in safety standards. While safety had started to become a bigger concern as early as the 1940s, there still weren’t many industry-wide or federally mandated protocols surrounding construction safety. Due to the increased risk that working with heavy machinery brought, protective equipment provided by companies became more commonplace, and federal initiatives around safety evaluation and reporting began to emerge. All of these changes paved the way for the safety campaigns that you’re likely familiar with today.
9/11 and Building Codes
The last and most recent event is, of course, the horrific destruction of the World Trade Center’s twin towers on the September 11, 2001, terrorist attacks on the U.S. At the time, it was almost unbelievable that these buildings, designed with cutting-edge technology and techniques, could collapse so easily. Certainly, other buildings had collapsed before—some even due to similar explosions, like the Oklahoma City Bombing that took out the Murrah Building—but what made the World Trade Center’s destruction especially terrifying was that it had been built specifically with safety in mind and were globally considered to be revolutionary feats of engineering.
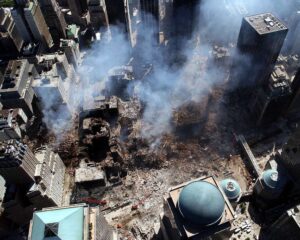
But there was a phenomenon behind the collapse of the towers that was little understood at the time, known as progressive collapse. Progressive collapse occurs when one or two primary structural components fail, but the adjoining components cannot handle the load and also fail, creating a chain reaction. Progressive collapse was known to be a potential problem with tall buildings in the aforementioned OKC Bombing, but it was not taken as a serious threat until the World Trade Center destruction.
As a result of the 9/11 disaster, there were two major changes to construction moving forward. First, building codes were updated to require higher standards for fire resistance in buildings over 420 feet tall, better fireproofing for buildings more than 75 feet tall, and elevators in buildings more than 120 feet tall.
Second, there was also an increased focus on strengthening the materials that compose buildings. One of the issues that led to the World Trade Center’s collapse was that the steel columns were melted and weakened once the fires caused by the plane crash reached 400 degrees Fahrenheit. Concrete, however, doesn’t experience any significant changes when it’s heated to that temperature, which is why the new One World Trade Center was rebuilt with reinforced concrete walls. Additionally, concrete used for high-rise buildings has since been reinforced with steel, preventing any cracking that might occur from an explosion.
Construction Today
We still feel the changes that these events from the past brought to the industry, and in many ways have even innovated upon them. And we’re already starting to witness the ripple effects of COVID-19 as the healthcare sector booms and buildings in other sectors change to accommodate new fixtures in society like hybrid work.